Nothing is left to chance with designer Nick Blunt at WeberHaus
Exclusive interview: UK WeberHaus designer
UK-based designer Nick Blunt, director of Urban Curve Architecture, works with WeberHaus designing high-performance homes. Here, he shares his expert insight on everything from the precision of prefabricated construction, to WeberHaus’s spectacular new show house in Germany
Construction
Please outline the key differences between English and German construction methods, highlighting how each system works.
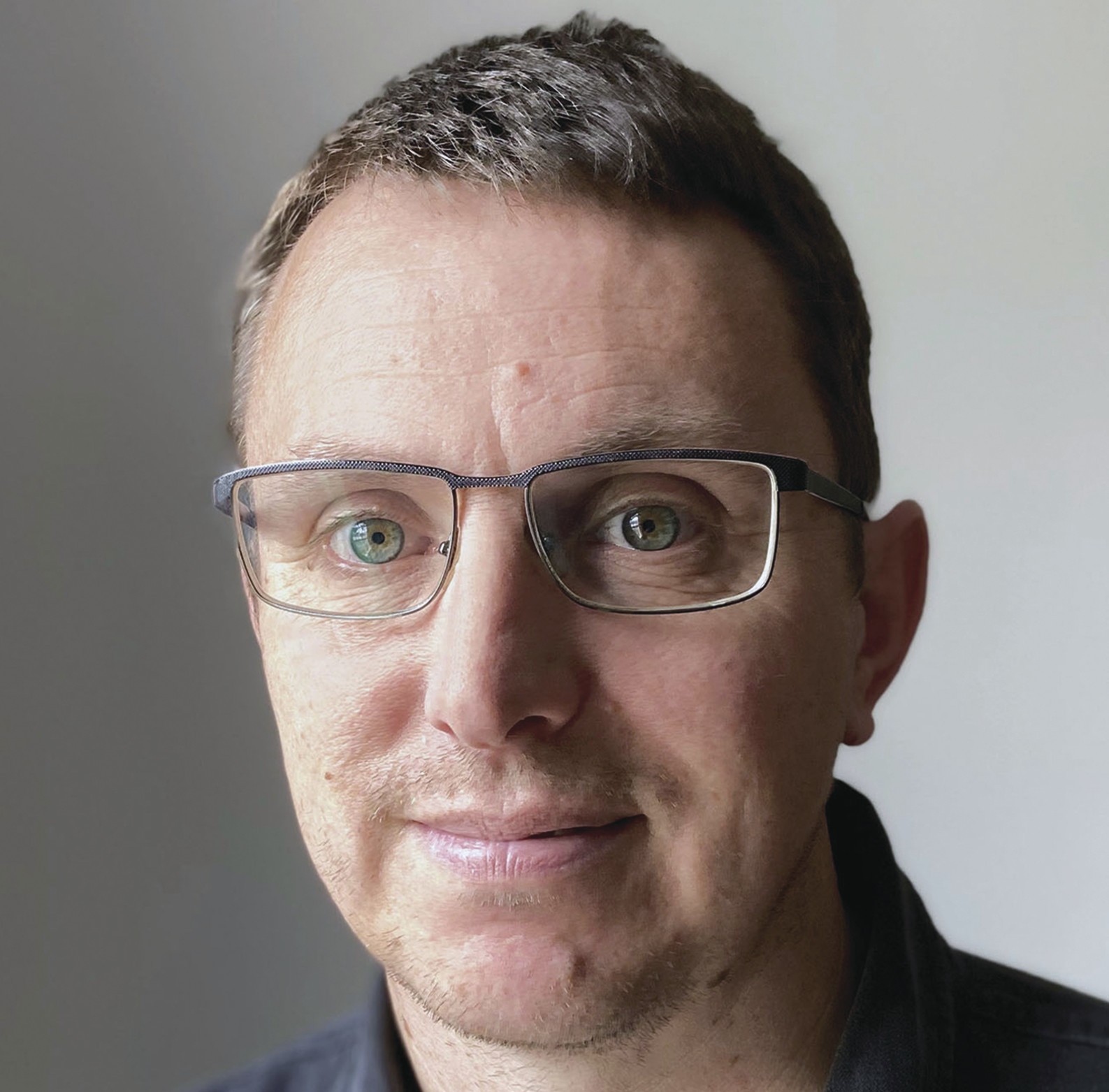
If we take brick and block construction as the typical English method of construction and compare it to the German offsite manufactured timber frame house, the biggest differences are in the superstructure, the build speed, precision and quality. Firstly, with the German form of construction, the slab is insulated and forms part of the building envelope. If you build traditionally in the UK with a beam and block floor, you’d normally insulate on top of that, so the mass of the concrete and the floor is cold and outside the thermal envelope.
Building with brick and block is obviously a slower process because it’s a wet trade and can therefore be significantly affected by the weather. You could be looking at a timeline of several months. On the other hand, the panellised German timber frame system is delivered to site and within four to seven days is erected to form a weathertight envelope. Brick and block is a cavity wall construction, so the space between the block layer and the outer skin of brick is partly insulated and partly cavity. Internally, you can either dryline or wet plaster the walls.
The German system is not a cavity construction – it’s a solid wall. The timber frame is fully filled with insulation and on the outside of the frame structure is wood fibre insulation. Externally, render is the most common finish. Internally, you have a wood panel and plasterboard finish.
What are the key advantages/disadvantages of these methods?
One of the key benefits of German construction is the improved thermal performance. The standard WeberHaus wall has a U-value (a measure of heat loss, where lower numbers are better) of 0.11W/m2K, which is to Passive standards. Brick and block only tends to just get above the UK Building Regulations, which depending on what you’re building, is down to 0.18W/m2K.
The German method also offers precision – everything is drawn to the nearest mm. Because construction is done under factory-controlled conditions, all the timber and insulation is completely dry when it gets built into the wall. The mastic around the windows is done in factory conditions, too, offering a higher degree of precision than you’d get on a rainy building site.
Plus, because of that high degree of German precision, you know you’re not going to lose heat through the building envelope. For example, you know the openings for the windows are going to be exactly the right size. They don’t have to be packed and adjusted on site because they were made to be the right size in the first place. As well as the swifter build speed you get with German timber frame, it’s ultimately more sustainable because your house is primarily fabricated from a renewable resource
Are there any particular circumstances in which one may be more suitable than the other?
Brick and block is potentially more resilient to flooding. However, the real answer to that is don’t build in a flood plain. In the past it’s been easier in the UK to get a mortgage on a brick and block house than it is a timber frame house. However, things are changing and there are companies out there like the Ecology Building Society that actively encourage you to look at alternative methods of construction, rather than brick and block
Prefabricated houses
What are the advantages of prefabricated houses?
Prefabrication improves speed and time on site. It also improves quality, because you’re manufacturing in consistent conditions and you’re not weather dependent. Repeatability is also another important factor. Although most the of the houses made in the UK are bespoke, the detailing is all repeatable. For example, if you’re building a one-off brick and block house, to a degree, it’s a prototype house – no one has built that design of house before with those materials. While a prefabricated house is bespoke, the detailing is still consistent. The manufacturer will always use the same window supplier, the same seal on the windows etc. You get the benefit of repeated standards throughout the house.
Another plus is that you’ve obviously got a dedicated, consistent construction team. While we handle the planning and Building Regulations side of things from the UK (more on this later), in Germany you have dedicated engineering teams, dedicated detailing teams – basically, the same people are working with the same types of details. While you’re reinventing the layout and bespoke elements, you’re not reinventing the detailing itself.
Because the teams have been doing the same thing for so many years, the process is streamlined, too. WeberHaus built 720 houses last year, and over the 60 years the company has been established that equates to about 40,000 houses. Over time that system has been refined, too, so clients essentially get the benefit of 60 years of product development
Advantages of WeberHaus
What makes it different from other German house building companies?
We’ve worked with several of the German house building companies in the UK, and I honestly think WeberHaus offers the most flexibility in terms of what they are willing and able to build. Some other companies work to grid systems, so you either need to design to that system or there is a cost penalty for not doing so. Other companies will also have greater restrictions on window openings and sizes. WeberHaus has flexible options for glazing in multiple heights. Of course, there are cost advantages for sticking to standard details, but it’s also a very flexible system.
My experience tells me there are fewer restrictions when we’re dealing with WeberHaus, in terms of non-standard details. There are other companies that will do a Passive wall, but I don’t think there’s anyone who will do a Passive wall as standard, like WeberHaus does. They also do triple glazed windows as standard.
Although they are flexible, WeberHaus would always encourage a client to use renewable resources where possible. Most of the houses will have air source heat pumps (ASHPs) or ground source heat pumps (GSHPs). However, gas systems are available upon request. The ASHPs and GSHPs work very well with underfloor heating, which come as standard in homes built by WeberHaus. That’s because this type of renewable heat source usually has an output temperature in the 40°C - 60°C range. Whereas, gas boilers operate at temperatures between 80°C - 95°C. Because underfloor heating operates at a lower temperature to conventional boiler-fed radiators, you actually get more efficiency with the heat pump solution rather than cross matching systems.
Mechanical ventilation and heat recovery (MVHR) systems are also included. They have benefits in that the heat exchange pre-warms fresh air that comes in, you get regular fresh air that can be filtered, which helps reduce your heat load in winter and your cooling load in summer.
Most of the houses WeberHaus builds have solar panels. We often put Tesla batteries into the properties, too. So you can, in theory, have a self-sustaining house because you can produce electricity, store it and use it to drive your heat pumps, which then power all your hot water and space heating. So, you can theoretically have a closed loop. There are customers who are energy neutral on an annual basis.
The sourcing of the products is also important from a sustainability point of view. The timber, which is the main product, is sourced from sustainable forests in Germany. We also factor in solar gain when we’re building houses. Obviously, because the houses are so well insulated and airtight, there’s no longer a need to worry about the house getting cold. What you need to think about is the possibility of shading the interior in summer. There are plenty of design choices when it comes to limiting the amount of solar gain the house gets, but any window within 45° of south would have external blinds, brise soleil or roller shutters. You can also incorporate external venetian blinds, which tilt to provide shade but also let light in
Health and wellbeing is going to be a very important factor in the future of our buildings. We’re already able to deal with factors like thermal performance, so now the focus is shifting onto the quality of air within the house. As standard, MVHR systems should be incorporated to ensure a fresh supply of air. You can also put special filters into this type of system to alleviate symptoms for sufferers of allergies. Incorporating construction materials that don’t have toxins is important, because you can reduce the off gassing of materials once the house is complete. The air is going to be pure and clear. The houses also tend to use hard flooring, which minimises dust build-up when compared to carpets.
One of the reasons Hans Weber set the whole company up in the first place was because back in the 1960s, there was an issue with cold, damp concrete buildings in Germany. He saw the potential to build a timber frame building that was well ventilated and constructed to high standards of thermal efficiency and knew it would be better for health.
Wood-built houses provide inherently high standards for healthy living and wellbeing. The independent, private Institute for Toxicology GmbH uses the latest technology to calculate indoor climate moisture, particles and germ collections, formaldehyde and VOC emissions. These assessments proved that even in a recently completed WeberHaus dwelling, the average values for formaldehyde are well below the specifications of the Working Group Ecological Research Institutes. All WeberHaus homes come with the “recommended for healthy living” certification, too.
Nick’s role working with WeberHaus
What is your role at WeberHaus and how do you work with future WeberHaus homeowners?
My practice, Urban Curve, has existed for nine years. For the first five years, we worked as freelance designers for several of the German and Swedish house manufacturers. We became WeberHaus’s exclusive UK design partner about four years ago.
The arrangement is that when one of WeberHaus’s clients needs planning, design and project management services in the UK, we set up a meeting. The client is not obliged to work with us, and some obviously come with planning permission for a scheme already. Some clients will have another architect they want to work with, so in that case, we can offer a flexible package where we only do part of the service. Essentially, we offer design work, planning, Building Regulations and project management services, as required.
Our work complements the package that WeberHaus offers, in that we can offer UK contacts for the elements that WeberHaus don’t do (e.g. groundworks). For clients looking for a faster, smoother process we have seen that our fully integrated service is very successful.
Please outline the key parts of your role, highlighting the process from planning, through to architecture and design.
Typically, we attend an initial client meeting with a WeberHaus sales representative to explain the system and how it works. Normally, the client would then appoint us to create their design concepts and take them through to planning. We then plan a house that is designed specifically to work with the WeberHaus system and liaise with the UK sales team and German project team to keep everything on track for the client.
Once we have clarified the client’s budget we involve WeberHaus further – particularly if there’s any non-standard things the client wants to incorporate. Once we’ve got a set of plans, we’ll submit them to planning. In parallel to that, WeberHaus do a costing exercise and will price up their part of the project, which is essentially the house above ground, fitted out. On our side, we’d talk to one of our established UK sub-contractors who we have worked with for many years about the groundworks side of things and get an estimate in for that.
Once planning permission has been obtained, we start with the remaining construction process. We have a role in preparing the UK side in terms of Building Regs, from the engineering drawings provided to us from the WeberHaus engineers in Germany. Urban Curve effectively manages the process up to the point at which the concrete slab inspection by WeberHaus takes place. Once everything has been checked, WeberHaus can start manufacturing the frame. Once the frame is delivered it goes up in three to six days, depending on project variations. By this point, the client often works with WeberHaus directly for the completion of the fit-out, but we can assist further on additional elements such as landscaping etc.
What is your previous experience in the construction industry and how does that feed into the work you currently do with WeberHaus?
I qualified as a chartered building surveyor in 1994. I worked in a practice that did surveying and residential architecture, which is when I moved across to the design side of things. I then worked for a developer and with private practices until I got to the point where I was working four days a week for the company, and one day a week for myself. It was at that point a client approached me about building a German kit house. From there, things developed over the years and I ended up working with several of the German house companies in my own time. In the end, I couldn’t do my own work and the work I had at the company, so I set up Urban Curve. I was introduced to WeberHaus, who about five years ago asked if I would design houses for them exclusively. Now, 60% of what Urban Curve does is therefore German prefabricated homes for WeberHaus
WeberHaus services & show house
For instance, what types of packages can homeowners choose from for their self-build? Is it just full turnkey packages or are other options available?
Turnkey packages are the norm. WeberHaus’s definition of this is that the house is completed above ground. In addition to the exclusion of the groundworks, the kitchens and light fittings would not normally be included in that. The logic behind that is that customers have more freedom to source a variety of kitchens and lighting in the UK – although WeberHaus can provide German kitchens, too. Alternatively, WeberHaus also offers a shell only package, which includes the frame, finished to the inside with the windows installed – effectively a weathertight shell without anything inside. There are also two incremental stages in between those two poles, which encompass a shell and services.
For example, you might have the shell without floor finishes, the final coat on the walls, internal doors and sanitaryware. That can be quite a cost-effective solution if you’re working to a budget, as things like internal skimming and floor laying are reasonably easy to source in the UK and it can be less expensive for clients wishing to manage this work themselves.
The key benefit is that the project management is coming from a single source in Germany. You’ll have a 3-4 day trip out to Germany where you pick all your fixtures and finishes with one of the company’s interior designers. You get the experience and level of detail with someone helping you through the process, and you’re covered by German guarantees, warranties and workmanship. Ultimately, you do pay a premium for the German quality and fit-out materials and the service provided. If you get a UK-based professional to come and install your doors, for instance, you’re obviously taking on more of the risk yourself. If there’s a problem, it’ll be your responsibility to fix. When you go for a turnkey package, there’s a single point of responsibility for the house.
As part of the celebration of WeberHaus’s 60-year anniversary, we submitted a design for a new show house about three years ago. All the architects that submitted entries had plenty of scope in terms of what they were able to design. In the end, ours was selected for the new house. It’s currently being built and is under wraps in the show park, where the company already has about eight other houses. The aim of the house is to show the potential for what could be built using the WeberHaus system.
It’s so important for inspiration and to see the high quality of the build. We often recommend to a customer that they should visit the factory in Germany before their sampling week where they pick their fixtures and fittings. It gives them the chance to understand what they will be choosing when they do go out there, and it’s a great opportunity to see and understand first-hand the culture of the company that will be building their next house.
By taking that initial trip, you will have a better sense of what the options are going to be. The factory visit is also a key step for clients to understand that it’s a very different way of building houses to the traditional English way.
We designed the house in a modernist style. It’s essentially a simple white rectangular form sitting over a box. We’ve got clerestory windows around the perimeter, so it looks like the upper storey is floating. The ground floor walls are covered in stone. There’s lots of glazing on the ground floor, too. Based on the architectural style of the house, you might assume it’s of concrete construction, so we wanted to incorporate several elements to show that wood is at the heart of the project.
Inside, there’s a little courtyard with a tree growing up through the centre – this is because we wanted to express that wood is at the heart, even though it doesn’t necessarily look like a timber frame house. We also incorporated a timber lattice as a sunscreen to bring more wood into the construction and remind people it’s timber frame.